Metal Fabrication is defined by Wikipedia as “The creation of metal structures by cutting, bending and assembling processes.” It’s central to what we do here at Garmendale and one of those traditional skills that underpins everything we create within theme parks, attractions and even the buildings that house the rides themselves.
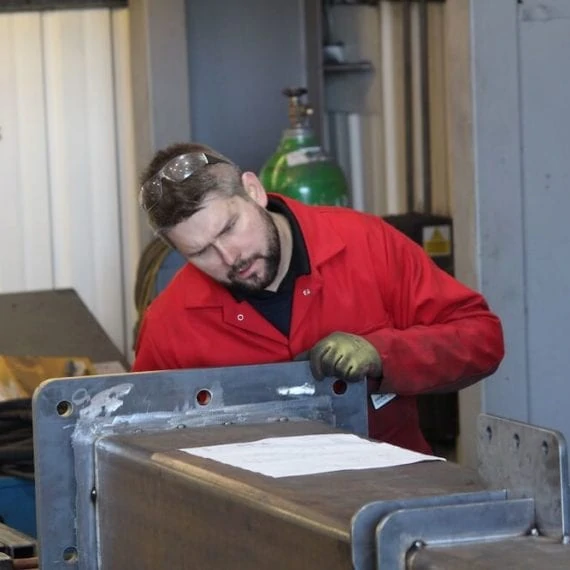
We wrote about this a while ago over here. The key for us is consistency in quality, reliability and traceability of materials. Without this, we wouldn’t be able to deliver work to the standard BS EN 1090. This ensures our work is independently tested and verified too, so when we claim we work to an agreed standard, we can prove it.
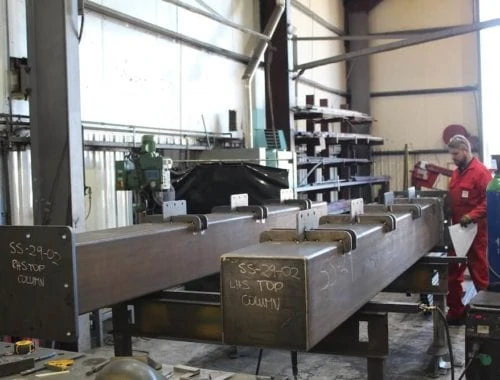
So, let’s look at those three pillars individually – Quality, Reliability and Traceability – and see what goes into them.
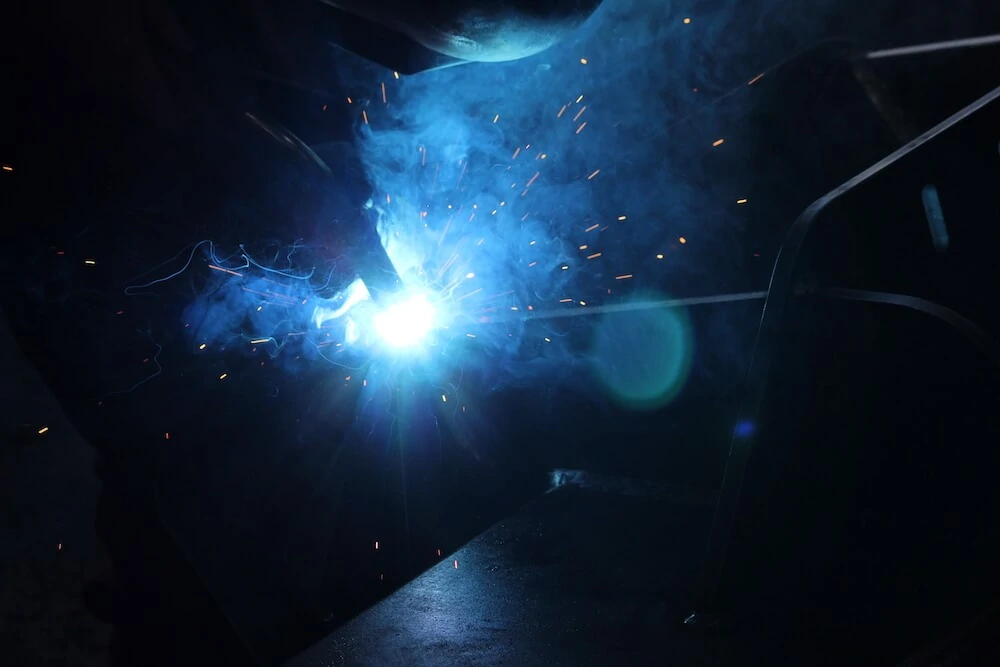
Firstly, Quality
This covers everything from materials, to the training of the team of fabricators, their welding skills and even the equipment and consumables they use. To deliver consistent quality, a corner can never be cut, without the risk of compromise. We train our welders to within an inch of their lives and can safely say that there are few in the UK or beyond that can weld to higher standards. Most of our designers have worked their way through the system as metal fabricators first and then trained for many further years to qualify as design engineers. Because of this, they have an intrinsic understanding of how metal behaves and where risks can creep in – before they even start the actual calculations to prove their thinking.
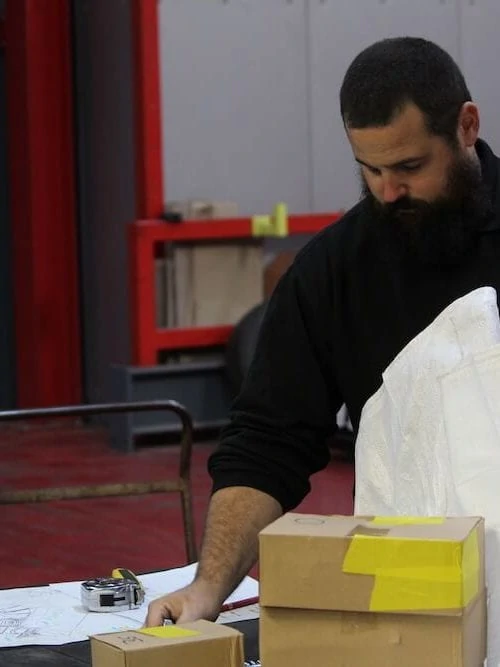
Reliability
We can assure reliability as all of our work is generally independently tested via a Magnetic Particle Inspection. This is a non-destructive testing (NDT) process that detects surface and shallow subsurface irregularities in ferrous metals. It ensures the welds are consistent and structurally sound throughout their depth, rather than just looking good on the surface.
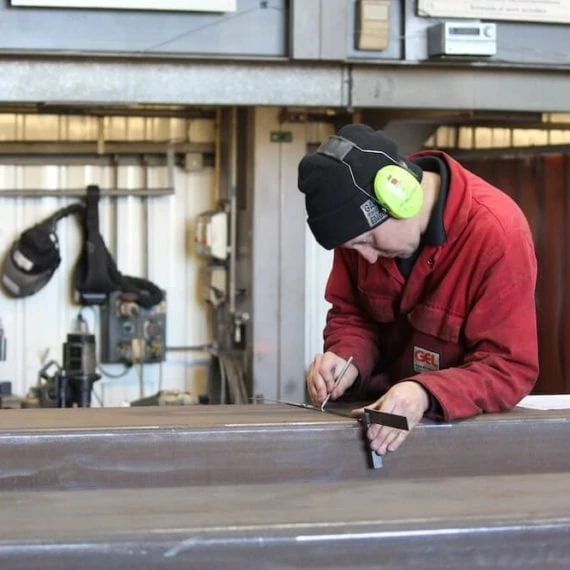
Traceability
There will always be a cheaper ‘pot’ metal around that for many, could be tempting to utilise in order to save a little in the material element of the build cost. We work with supply partners who verify their supply chain. Our steel is often British, but always from a mill that certifies the quality of the metal they produce, so we can in turn pass that certification onwards, safe in the knowledge that it’s valid.
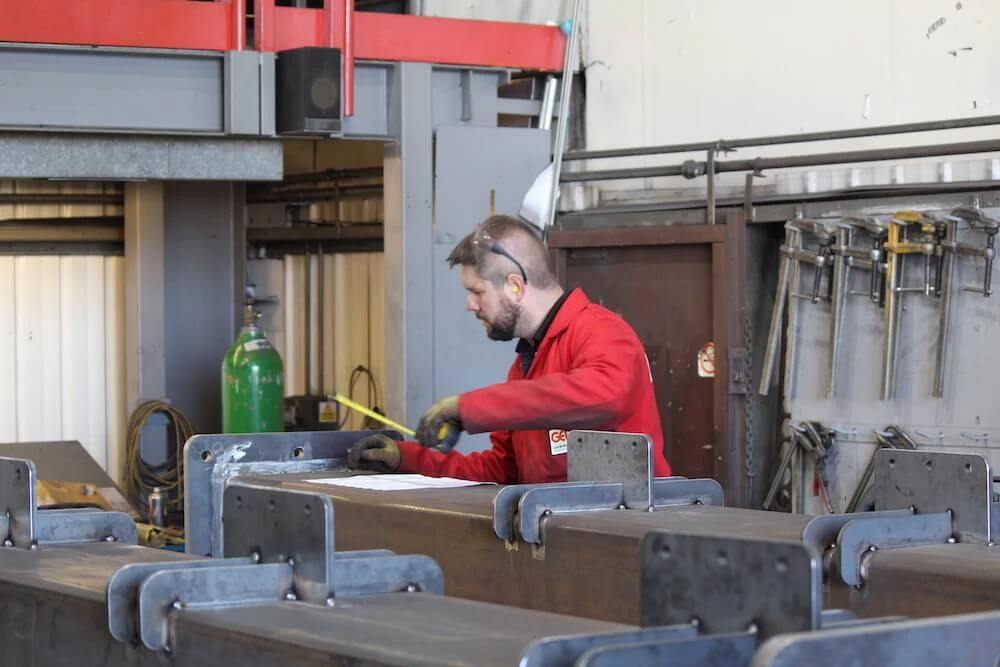
When you see unfortunate incidents in the news where a structure has collapsed, it’s invariably due to one or all of these three pillars being compromised, but they are nearly always preventable.
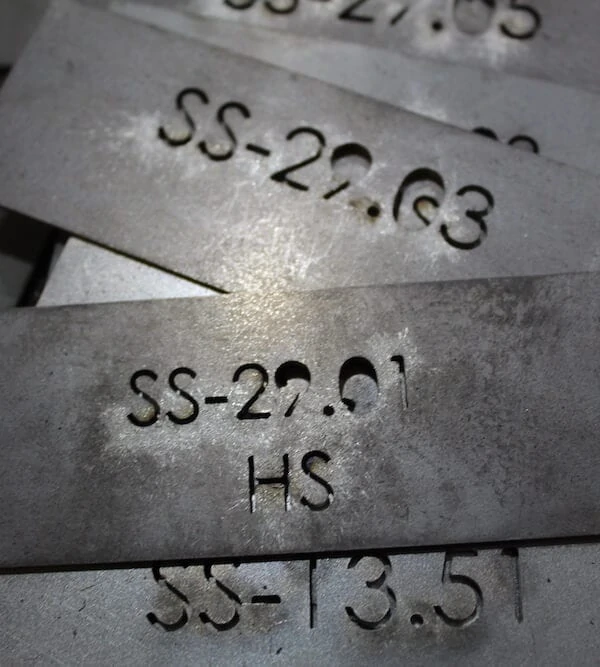
We’ve been metal fabricators for nearly 40 years and intend to be here for many years in the future. Metal Fabrication is at the heart of our culture and the centre of our business. It’s not the most glamorous side of our work, but we love it and without it, the rest wouldn’t be possible.
And if you’re interested, here’s a little more about the BS EN Standard 1090.